
If you read or follow any polymer clay groups and forums, you’ll notice that one of the most common questions asked is “Which polymer clay sealer should I use?” Everyone has their favorite sealer, and the answers differ depending on your need and the availability of products where you live. But perhaps we’re asking the wrong question. I think the first question needs to be, “Do You Have to Seal Polymer Clay?”
Do you have to seal polymer clay?
- You don’t have to seal polymer clay. Baked polymer clay is durable plastic and therefore more durable than any sealer.
- Sealers and varnishes will not prevent breakage. If your projects are brittle, address your baking process.
- Use a varnish to protect fragile surface treatments such as chalk, pigment, or mica.
- Use a varnish to change the gloss level of your project.
- Many varnishes make polymer clay sticky. See here for more info.
- Spray varnishes are nearly always incompatible with polymer clay.
- For a glass-like finish on plain polymer clay, sanding and buffing is an excellent option.
When to Seal Polymer Clay
People often want to seal their polymer clay creations for protection against the elements or from damage during use. In most cases this is unnecessary. Once it’s been properly baked or cured, polymer clay becomes a durable solid plastic that is waterproof, shock resistant, and fairly tough. Because it’s such a durable material, it probably won’t surprise you to learn that it’s actually more durable than any sealer that you will put on it. Sealers, varnishes, and finishes do have their purpose, but bare clay itself does not need to be sealed for protection. Here are some reasons why you would want to seal polymer clay:
Protect Surface Treatments
When you embellish your polymer clay project with chalks, paints, mica powders, metallic pastes, or metal leaf, those treatments are sitting on the surface of the polymer clay and are not nearly as durable as the polymer clay itself. Projects using surface treatments must therefore be sealed for maximum durability. In the case of jewelry, the wearer must also be protected from any pigments, dyes, and mica coming off on their clothes or skin. If the project is purely decorative and will merely be sitting on a shelf, sealing is not imperative. But keep in mind that cleaning any accumulated dust would likely cause the surface treatments to be disturbed.
Polymer clay artists often use acrylic paint to color and embellish their projects. Does acrylic paint need to be sealed? Well, it depends. Paint used to antique a textured surface is mostly rubbed off and the remaining paint is fairly well protected down in the “nooks and crannies” of the piece. In that case, I would not seal it. But thin layers of acrylic paint can sometimes peel or scrape off or will come off if the piece is washed. In those cases, I would use a sealer. Even when the layer of paint is thick and strong, a sealer might give a brighter, more durable coating much in the same way that a clear coat is used over the colored paint on your car. You’re going to be the best judge for your own particular project.
Change the Gloss Level
Although different brands of clay have different native gloss levels, and the technique you use can leave you with a matte or glossy surface, the easiest way to change the gloss level of your finished piece is to use a sealer that has the desired type of gloss level. Many varnishes come in both glossy and matte varieties. Sometimes you will look at a finished piece and realize that you would like it better matte or glossy and choosing the correct varnish can easily give you the effect you want.
Ease of Cleaning
Polymer clay is not porous like wood or unglazed ceramic. It will not absorb and hold water. Polymer clay can, however, have fine pits on the surface, depending on the method you used to create the piece. Some clay brands, such as Sculpey III and Souffle, tend to have a surface that appears to be porous (this is also why those brands are so great for holding onto acrylic paint). Because of this, dirt and makeup may be difficult to remove from a piece without scrubbing with soap and water. This can also be a problem when the clay is created with a finely textured surface. Plus, sometimes the dyes in your makeup can permanently discolor light-colored clay beads. In these cases, sealing the clay makes sense.
Intensify Colors or Translucency
Just like a pebble dipped in water becomes more vivid and bright, a coat of sealer can make polymer clay appear more rich, deep, and colorful. This also holds true for translucent clays. They will appear even more translucent when a sealer is used on the surface.
When NOT to Seal Polymer Clay
Sealers and varnishes are wonderful tools to be used when the time is right. But there are reasons why trying to seal your project might not be a good idea. Here are a few reasons.
- Many sealers, varnishes, and coatings turn sticky or cloudy over time, ruining your project. What works for one person might very well not work for another. Unless you know how your chosen sealer is going to act, and unless you’re certain you need to be using a sealer in the first place, it might be better to reconsider. Always test some samples before using a sealer on something that’s irreplaceable.
- Because most polymer clay varnishes are, themselves, a kind of thin plastic coating, they can often be peeled from the project if you try hard enough. If the product will get lots of abuse, a varnish might not be strong enough.
- When making glass-like items, using a gloss sealer is not a substitute for creating a smooth item in the first place. Applying a glossy coat over the top of a project full of tool marks and fingerprints will just accentuate them rather than camouflage them, making your project look sloppy and unprofessional.
- Using a sealer on a highly textured item can go badly wrong. I remember waxing my dad’s pickup when I was about 10. I got wax on the black plastic trim. Of course, it turned white in the grooves. Bad memories! Polymer clay is no different. Wax is great for smooth surfaces, but it will collect in the small crevices of a textured item and look awful. Liquid varnish such as Varathane will also collect or pool in highly textured areas, leading to a look that very much wasn’t what you had in mind. You can seal textured items with a varnish, but you have to be careful in your application. Don’t just slather it on!
Use the Right Sealer for your Project
There are lots of types of polymer clay sealers and glazes. I use a different sealer depending on the effect I want to accomplish in my finished piece. There are many excellent varnishes, finishes, and sealers out there, and I haven’t tried them all by any means! But here are some tried and true sealers that I can heartily recommend.
Some of the links below support my work by earning an affiliate commission if you purchase using them. This is how it works.
Glossy Sealers
Varathane is a brand name of polyurethane varnish available in the US. It has been a favorite varnish with polymer clay artists for many years. It does come in gloss, semi-gloss, and satin, but I find that even the satin is still pretty glossy. I wrote an article about Varathane describing why it’s my favorite sealer and giving sources (including non-US brands of polyurethane).
Pearl Ex Varnish is made by the same company as the well-known mica powders. But this is just a varnish. It works nicely on all brands of clay, but doesn’t give a super glossy finish.
Aleene’s Jewelry Pendant Gel is a glossy dimensional glaze that can be used on most clays, but avoid using it on Fimo as it can get sticky.
Epoxy Resin is a clear, thick coating that is gaining popularity among polymer clayers, for good reason. It is exceedingly strong and durable, more so than any other finish. But it has a long cure time, takes some practice to get used to using, and is known for causing swear words. But once you get the hang of it, it works very nicely. Favorite brands are ICE Resin, Envirotex Lite, and Magic Glos (a brand of UV-cure resin).
Kato Liquid Polyclay can be used as a sealer. Just brush or sponge on a thin coating and then cure in the oven. After oven curing, you can use a heat gun to further cure it to give a crystal-clear, glossy finish.

Matte Sealers
Translucent Liquid Sculpey is another brand of liquid clay but this has a matte finish when cured. To get this effect, use a cosmetic sponge to dab the TLS onto your piece, then oven cure. Do not cure with a heat gun or the effect won’t be matte.
Cernit Matte Varnish gives a nice, smooth, dry finish on all brands of clay. It’s not terribly matte, but does give a low-sheen satin finish that looks and feels great.
DuraClear Ultra Matte Varnish is a dead matte varnish that has no sheen at all. It performs beautifully on all brands of clay except for Kato.
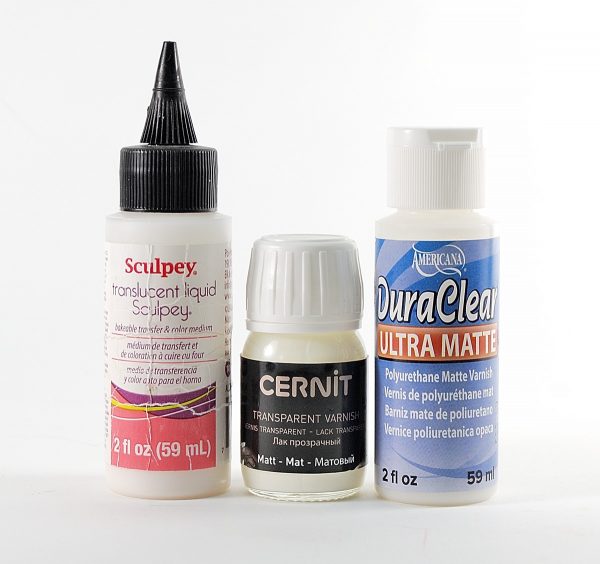
For a Natural, Burnished Look
If you like the look and feel of polymer clay that’s been sanded to a very high grit and buffed, you will love the way that adding a coat of wax makes those pieces feel and look. Renaissance Wax is a favorite brand of high-quality wax that has a great marketing program and a price tag to match. Don’t get me wrong, I love Ren Wax. But want to know a secret? Paste Wax and Neutral shoe polish will work just the same and have a MUCH better price. Remember, wax doesn’t work well on items with a fine texture (such as when you use sandpaper or a sponge to disguise fingerprints). The wax will collect in the pits and look awful.
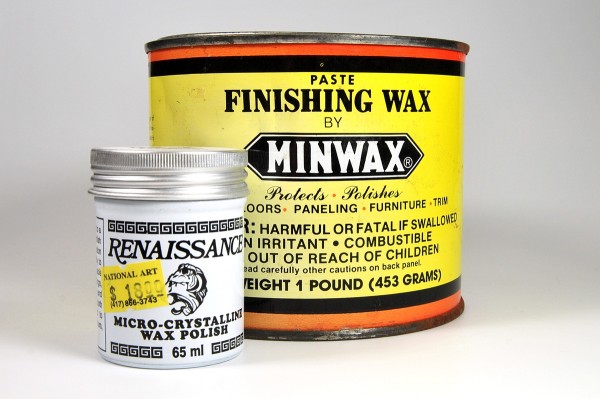
Sealers to Avoid
Just as there are good sealers on the market, there are also some bad ones. Keep in mind that many of these have been used by many people without any ill effects. But they are also known for having unsatisfactory results as well.
Future Floor Finish, which is now called Pledge Floor Care (and is very similar to the European product Klear) is a very clear, thin, watery finish that is a favorite of beginning polymer clay artists. It gives a nice glossy finish, dries clear, smells great, and is readily available. I used it when I first started and I don’t really have much bad to say about it, except that it’s not very durable. There are better options, such as any of the sealers I mentioned above. It’s still a good sealer for things that won’t get any wear, such as figurines and models. But for jewelry, it just dulls down way too fast.
Liquitex Varnish, which I have previously recommended, is an artist’s varnish that comes in gloss, matte, and satin finishes. My tests show, however, that it has lots of brush strokes, turns cloudy on dark colors, and is sticky on some brands of clay. There are better options, such as Varathane or Pearl Ex Varnish.
Dimensional glazes are thick, clear one-part glazes that can be applied thickly to create a glossy, glass-like finish. Some are better than others, but all of them can turn cloudy over time. I think that humidity is a factor. Some brands are Triple Thick, Diamond Glaze, Dimensional Magic, and Aleene’s Jewelry and Pendant Gel. I have found that all of them turn sticky on at least one brand of clay. Aleene’s did show good results on every clay besides Fimo, however, so you might try it. For every person who recommends Triple Thick, I read of another one who says it gets sticky or cloudy. And the reviews I’ve read of Dimensional Magic are sad. I don’t like reading of people’s projects being ruined by a material that was used properly! Success is just too variable with these glazes for me to recommend them universally, aside from Aleene’s.
Nail Polish is often recommended as a paint or glaze by articles in craft blogs. Almost always there will be tears later because the plasticizer in polymer clay softens the polish, making it turn gooey over time. That is, if it dries at all. The thing is, it can be rather hit and miss, perhaps due to the brand of clay or nail polish. It does work often enough that people not knowledgeable in polymer clay will not see what’s wrong with recommending it, and the next person isn’t so lucky! If I had a dollar for every email I answer on this one…
Oil-based Varnishes will often work on polymer clay but will yellow noticeably with time. Cindy Leitz tested Minwax oil-based polyurethane and found that there were no compatibility issues with polymer clay, but it did yellow. This is most noticeable on white clay, of course. Cindy’s result does show the value of testing and making samples. Don’t just randomly grab any can of varnish from the hardware store shelf.
Mod Podge is a glue and decoupage medium that crafters have relied on for working with paper for as long as I can remember. Craft blogs also sometimes recommended it as a sealer for polymer clay. Just don’t do it. No. Mod Podge is actually made from the same stuff as plain white glue. It’s not a real sealer. You wouldn’t coat your beads in glue, would you? Again, some people have good results with this. But for most of us Mod Podge gets sticky and cloudy in humidity. Just say no.
Spray sealers can also have unpredictable and disappointing results. Sometimes the finish never dries, other times it turns soft and sticky months later. It seems that the plasticizer in baked polymer clay can soften the spray varnish, so even a good trustworthy brand of liquid varnish might not work so well in the spray form on polymer clay. If you need a spray, do yourself a favor and order some PYM II. It’s one of the few sprays that I know of which is absolutely safe to use with polymer clay. Your mileage may vary, of course. I tested 10 different brands of spray sealers and found that only PYM had universally good results on all the brands of clay that I tried.
Sealing Myths
New clayers often assume that polymer clay needs to be sealed to protect it against water damage. Cured polymer clay is waterproof and does not need to be sealed against moisture. Most sealers are not fully waterproof (they’re merely water-resistant) and can be damaged by prolonged contact with moisture. (A quick wash is not usually a problem for a sealer, though.) If you’re using polymer clay to decorate the outside of drinking glasses, you do not need to seal the polymer clay to make it safe for washing. You do, of course, want to hand wash any decorated glassware, but that’s true for any hand-embellished glassware. Dishwashers can be pretty harsh.
If you’re making a polymer clay project for use in aquariums or outdoors, a sealer is not only unnecessary but will most often deteriorate well before the clay. Polymer clay is weatherproof and will not crumble or fall apart after exposure to the elements (see the picture of my hearts, below). But the color of some clays can fade in sunlight. I would like to say that a UV sealer will protect your work, but I do worry about the durability of the sealer itself in outdoor conditions.
Another myth is the belief that a sealer will protect a weak polymer clay sculpture against breakage. A coating of varnish or sealer will not make your piece stronger. It will not prevent pieces from breaking off. If small pieces such as ears or arms are not properly adhered in the first place, a coat of sealer will not help things stay in place. The first time the piece is dropped or roughly handled, the ears will snap right off. I suppose if you coated a piece in a thick layer of resin, it would offer structural support. But it would also look pretty gloppy.
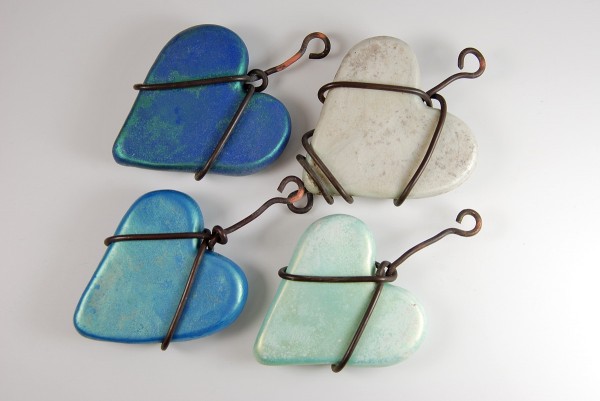
Tests and Samples
Regardless of what anyone tells you, though, it’s always best to test any new materials or techniques yourself before you commit to using them with a large or special project that you have put a lot of time into. That way you find out about the problems before anything gets ruined. For instance, Varathane is a fantastic sealer. But you have to learn how to apply it without creating bubbles, and the best way to do that is to do some tests and see what works best for you. Each sealer that I do recommend will come with its own quirks and challenges. Testing and doing sample pieces will help you find the best ways to use them.
Also remember that if you’re selling your work to others, your reputation as an artist depends on the long-term quality of your work. You owe it to yourself and your customers to make sure any sealers you use will hold up over time. Here’s a great article by Staci Louise Smith about how important it is to test your jewelry before you sell it to a customer.
And now I have a favor to ask of you. If you’re reading groups and forums where beginners are dealing with the frustrations of a badly chosen sealer, would you mind pointing them to this post? Maybe we can get the word out there and prevent some sticky beads!
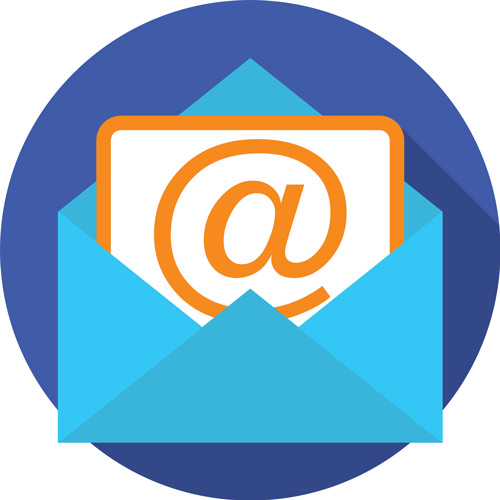
Email is the best way
to get updates
You will LOVE getting this email, which is packed full of polymer clay goodness. About once or twice a month.
301 thoughts on “Do You Have to Seal Polymer Clay?”
I have ordered a plant pot from an artist who has used polymer clay. She has baked it directly onto a glazed pot (or it could be a porous terra cotta). Am I safe to assume that she has not used any glue or sealer? I guess i’m just trying to gauge how durable the plant pot is since it will hold a plant and get watered and misted regularly. Not much different than the outdoor exposure you refer to. I realize it may be difficult for you to know with certainty without seeing the piece. I guess what am I asking is would it have been necessary to glue or seal a plant pot? Thank you for the great and honest information you provided. Very informative.
The maker of the pot would be the best person to address this because she knows how she made the pot. I would just be guessing. Also, if the pot deteriorates when used as a plant pot, the maker should address it. Makers very much value that kind of customer feedback.
Hello, thanks for all of the info. I have a question. I made a pottery mug and on the inside the glaze crawled leaving bare clay. I was told that I can use polymer clay to fill in these voids. Should I use one of the sealers you mentioned since coffee will come in contact with it? Also I baked the mug but it doesn’t look like the clay melted. I put it in for 5 more minutes twice. I don’t know how it looks when it is baked correctly. Perhaps it is fine and I don’t know it! Thanks.
Sadly, the information you were given is wrong. Polymer clay cannot be used for food contact. It is not a suitable material for this purpose.
Polymer clay doesn’t melt when it’s cured. It’s a modeling clay that keeps its form when it cures.
I’m pretty sure the only real solution is to refire the mug. The glaze will change, however. It’s best to consult the folks that helped you fire the mug in the first place. They’ll have info on re-firing.
Thank you for the article on sealers and gloss enhancers. I have a few test pieces, made from scrap clay and painted with acrylic paint, that I sealed with Acrylic Spray Gloss. They are tacky to the touch and have not cured. Is there a way to salvage them? Can I overcoat them with resin or something like varathane? What do you recommend please?
If it’s only a tiny bit tacky, you can usually coat with Varathane and it will be fine. But if it’s super goopy, you need to remove the coating. Isopropyl alcohol will help with that, but it will also strip the paint and make things look pretty rough.
I’m in shock at your article! It’s so detailed and informative. I can’t believe I can make little pots and plant my plants direct in them! I wondered about this for years, never having time to look into it. Your article is the first I read and will just go with it. Thanks for taking time to provide this and for free.
Great article! What about colors fading I was hoping to put a sealer on it to stop the colors from fading the figures are in a room no natural light only light is if I turn on the light bug it’s on only a short time. Also they seem to be more brittle like they’re drying out. Can you mist them does that help?
Sealers don’t protect from fading. Polymer clay figures don’t dry out and if they’re brittle, they are underbaked. Misting will not help. Polymer clay is vinyl plastic. Perhaps I misunderstood what you are asking, though.
Wow!!! I love all this information!! Thanks so much for putting so much work into these details and the links between articles! I’m SO GLAD I found you and your info!!! I’ll be back 🙂 and I also love that you don’t HAVE to seal it…. I started noticing I loved how the finished clay looked and felt by itself!
YES! Polymer clay has a lovely feel all by itself. You’ve probably noticed that I’m a big fan. BTW, welcome!
This is such a helpful article. Thank you for sharing,
Hi Ginger,
I have an issue where my clay beads become dirty…perhaps from sweat, some makeup & oils from the skin after wearing them for a couple weeks. I tried to scrub it with soap & water many time and even rebuff the surface but it won’t go away:(
I use fimo, sand & buff to shine. Are there any other cleaning methods I should try or is it best to just seal it? I love the way the baked clay looks after it’s sanded with a high grit and buffed…which sealer should I be choosing if I should seal it at all?
Thanks so much for your detailed post & blog! It’s really a life saver every time I have an issue working with clay!
Yes, this can be an issue for sure. Light colors can easily stain as they “absorb” dyes from clothing and makeup. You could try scrubbing them with alcohol (but only if they don’t have any surface treatments or varnishes.) But yes, sealing is often the best solution here.
Hi, thank you for a great article!
I have made earrings with gold leaf that I plan to seal with Cernit Matte Varnish. It says on the bottle that it needs to be baked to seal properly. I then use sculpey liquid clay (which also needs baking) to attach my earring posts.
In which order should I apply and bake the varnish and posts, I guess the earrings have to go in the oven 3 times??
Thank you and have a great day!
Bake the backs first. Varnish is the final step.
Hi, I’ve been looking everywhere for advice on this but I haven’t had any success. I just used acrylic paint to stencil onto raw polymer clay, and now that it’s baked the paint is a kinda tacky, do I need to seal these?
Sealing might help with the stickiness. But the problem is the paint. Have a look here.
I’ve read that article before and it wasn’t taking about acrylic paint on raw clay, it was talking about painting on baked clay, that makes a difference right?
You do have paint on baked clay. It doesn’t matter that it was applied to raw clay first. The paint is reacting with the polymer clay and has softened. It will always be sticky. It’s incompatible paint. As I wrote in the painting article, if it’s a tiny bit sticky you can coat with Varathane and often solve the problem, but if it’s super goopy, it won’t help.
Gotcha, thanks you!
Hello. Forgive me if this has been asked before. I make pendants out of mostly Premo polymer clay, but also some others mixed in. While nail polish is not recommended to go directly on cured polymer clay, can it be safely applied (to not compromise long term hardness) if the piece is first dipped in acrylic Varathane to act as a barrier between the clay and the polish? Thank you so much for your extremely useful tips!!
No, Varathane will not be a barrier to plasticizer migration. Many brands of nail polish will still be affected by the plasticizers in the polymer clay.
Comments are closed.